Comprehensive Guide to Choosing the Right Fluoropolymer
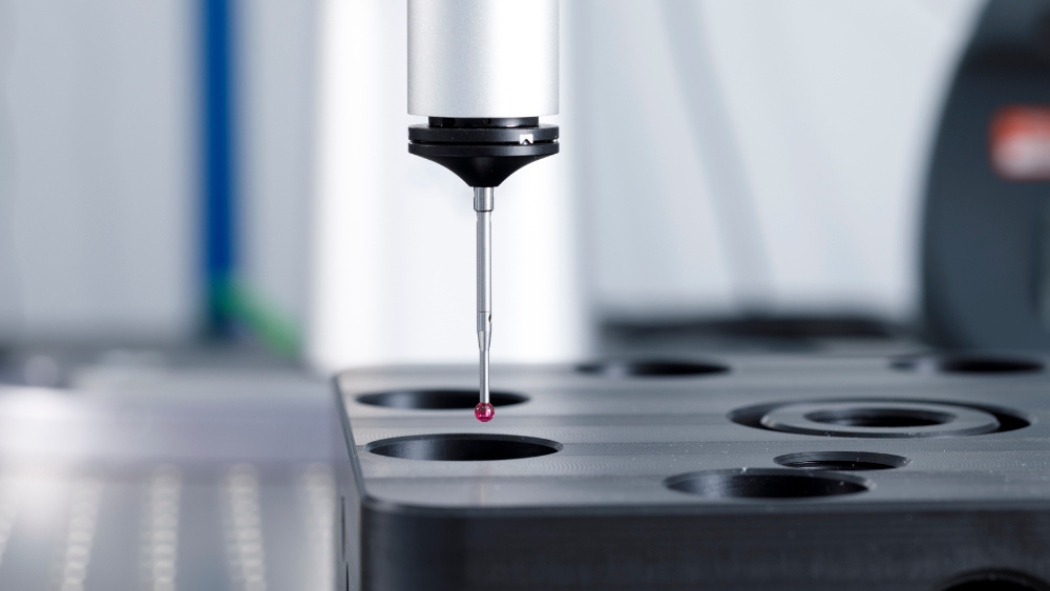
Selecting the appropriate fluoropolymer for a specific application is a critical decision that can significantly impact the performance, durability, and cost-effectiveness of engineering components and systems. Fluoropolymers represent a unique class of synthetic polymers characterized by their exceptional chemical resistance, thermal stability, and low friction properties, making them invaluable across numerous industrial and technological domains.
The fluoropolymer selection process begins with a comprehensive understanding of the specific environmental and operational requirements of the intended application. Each fluoropolymer variant offers distinct characteristics that make it more or less suitable for particular uses. Polytetrafluoroethylene (PTFE), perhaps the most well-known fluoropolymer, stands out for its remarkable chemical inertness and extremely low coefficient of friction. This makes it ideal for applications requiring non-stick surfaces, such as cookware coatings, medical devices, and specialized industrial components that demand minimal friction and maximum chemical resistance.
Perfluoroalkoxy alkane (PFA) represents another critical fluoropolymer variant, offering enhanced processability compared to traditional PTFE. Its superior melt processability allows for more intricate part designs and better flow characteristics, making it an excellent choice for semiconductor manufacturing, chemical processing equipment, and high-purity fluid handling systems. PFA maintains exceptional thermal stability and chemical resistance, ensuring reliable performance in extremely demanding environments where other materials would quickly degrade.
Fluorinated ethylene propylene (FEP) provides yet another compelling option, bridging the gap between PTFE and PFA. Its unique properties include excellent electrical insulation, outstanding transparency, and remarkable weatherability. These characteristics make FEP particularly valuable in wire and cable insulation, architectural membranes, and specialized medical tubing where visual clarity and environmental resistance are paramount.
When evaluating fluoropolymer selection, engineers must carefully consider multiple factors beyond basic material properties. Temperature range, chemical exposure, mechanical stress, electrical requirements, and manufacturing constraints all play crucial roles in determining the most appropriate polymer. For instance, a fluoropolymer used in aerospace applications must withstand extreme temperature fluctuations and potential exposure to aggressive chemical environments, while a medical implant requires biocompatibility and minimal reactivity.
Cost considerations also significantly influence fluoropolymer selection. While these advanced materials offer extraordinary performance, they typically command a premium price compared to more conventional polymers. Balancing performance requirements with budgetary constraints demands a nuanced approach, often involving detailed cost-benefit analysis and long-term reliability projections.
The manufacturing process represents another critical aspect of fluoropolymer selection. Different polymers exhibit varying processability, which impacts fabrication techniques such as molding, extrusion, and machining. Some fluoropolymers require specialized equipment and expertise, potentially increasing production complexity and expense.
Advanced characterization techniques, including thermal gravimetric analysis, differential scanning calorimetry, and spectroscopic methods, provide invaluable insights into fluoropolymer performance characteristics. These analytical approaches enable engineers to precisely evaluate material suitability, predicting long-term behaviour under specific operational conditions.
As technological demands continue to evolve, fluoropolymer research persistently advances, introducing increasingly sophisticated materials with enhanced performance characteristics. Emerging variants promise improved thermal stability, enhanced mechanical properties, and more sustainable manufacturing processes, expanding the potential applications for these remarkable synthetic polymers.
For more information on how Dalau can assist you with your project, please get in contact with us today for an informal chat.